Forget the Dremel I use a Power Drill!
You use a wire wheel to port your manifold and ports, I welded an extension shaft to mine, your ports should look something like this

Beware there are pit really big falls with EFI systems.
1. WOT fuel delivery a 2000 cc engine needs 1000 cc/min carby seems to handle it some how.
2. Flap airflow meters would go off scale too.
Beware the timing needs to be tuned as carbon builds up.
I have a laptop interfaced to my second engine with my own program.
eg computer controls the engine timing and 2 stage rev limit.
The timing is linear with rpm as far as I can tell to 7200 rpm I think this is a good thing.
eg plot a line 0 deg at 400 and 35 deg at 10000, 6000 is about 20 deg from memory.
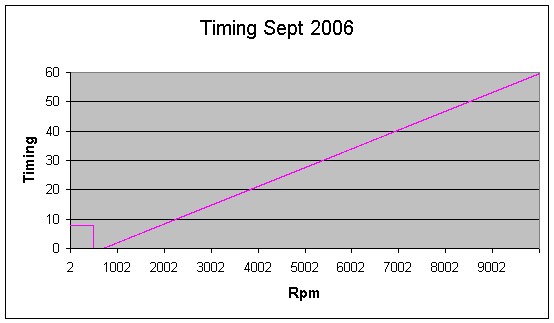
If anybody has a flow bench handy you could bore out PVC pipe as a test, before cutting into any alloy head.
Things like feed rate in and out of the tube would have to be noted
I have a 1986 Nissan Bluebird wagon 2000 cc (no EFI on this one)
I have tested fuel efficiency at idle and its in the range of 10 to 13 c.c./minute running a mixture of normal to slightly rich.
I have the test video's on Youtube you can go to my web site to see the 5 clips there,
http://ampair.tripod.com/Fuel.htmlFrom what I have read a normal 2000 cc engine at idle consumes 24 to 26 cc of fuel per minute.
I have improve fuel efficiency under highway driving conditions, I have experienced as high as 60 mpg (4.71 L/100km) over a 220 km journey on a hot summer's day cruising around 80 km/h.
I have a stock carby and my vac sec are fully open at 2000 rpm
it used to be approx 4000 so I can only guess at the air flow.
I have high fuel consumption in the high rev range with load though.